views
How Hull Corrosion Impacts Ship Performance and Longevity
Most of the world's goods are transported via ships, making the maritime industry a backbone of global trade. However, maintaining the efficiency and longevity of these vessels is no small feat, with hull corrosion being one of the most pressing challenges marine engineers, naval architects, and shipowners face.
But what exactly is hull corrosion, and why is it such a vital issue for the industry? Hull corrosion occurs when the ship's surface reacts with environmental factors, primarily seawater, leading to material degradation. This seemingly inevitable process doesn't just compromise the integrity of the vessel; it can dramatically affect performance, increase operational costs, and reduce a ship's lifespan.
This blog explores how hull corrosion develops, its substantial impact on performance and longevity, and the best prevention methods. Additionally, we'll look at case studies that highlight the challenges and solutions to this pervasive problem. By the end, you'll understand why prioritising hull corrosion management could save costs and enhance maritime operations.
Causes of Hull Corrosion
Understanding hull corrosion begins with identifying its causes. Hull corrosion types primarily occur due to the ship's exposure to the maritime environment. These factors below play a significant role in the degradation process:
Seawater's Corrosive Nature
Seawater is highly corrosive due to its salinity, with dissolved salts accelerating metal oxidation. This reaction occurs when seawater comes into contact with the iron or steel used in ship hulls, causing rust (iron oxide). The degree of corrosion depends greatly on temperature, oxygen content, and the concentration of minerals in the water.
Microbial Influence
Microbial-induced corrosion (MIC) is a silent yet potent threat. Certain bacteria, like sulphate-reducing bacteria (SRB), thrive in marine environments. These bacteria produce hydrogen sulphide as a by-product, which speeds up the corrosion of metal surfaces, particularly in water-ballast tanks and other submerged areas.
Galvanic Corrosion
Galvanic corrosion occurs when two metals with different electrochemical potentials are in contact while immersed in an electrolyte, such as seawater. This electrochemical reaction causes the more reactive metal (anode) to corrode faster while protecting the less reactive one (cathode). This is a common challenge in vessels with mixed-metal construction.
Poor Coating Maintenance
Even though anti-corrosion coatings make up the first line of defence, wear and tear over time exposes the hull's surface directly to seawater, leading to accelerated corrosion.
Atmospheric Conditions and Fouling
Ships operating in humid and varying temperature conditions often experience oxidation due to condensation. Additionally, biofouling from marine organisms such as barnacles and algae can trap seawater against the hull's surface, exacerbating corrosion beneath fouling layers.
Understanding these causes reinforces the need for proactive measures in maintaining a ship's anti-corrosion systems.
Impact on Ship Performance
The effects of hull corrosion on ship performance extend beyond material degradation; they directly impact operational efficiency and costs. Here's an overview of how various performance metrics are influenced:
Increased Drag
The roughened surfaces caused by corroded or fouled hulls significantly increase drag. When a smooth hull surface becomes uneven due to rust or marine growth, the ship must expend more energy to move through the water, making propulsion less effective.
Higher Fuel Consumption
One of the more measurable impacts of hull corrosion is the increased fuel usage. Studies estimate that a hull fouled by biofilm and rust can lead to a rise in fuel consumption of up to 40%. This erodes profitability and adds to the maritime industry's carbon footprint.
Reduced Speed and Maneuverability
The increased drag from hull corrosion can also lead to reduced sailing speeds. Achieving the same speed requires greater power, often overburdening the engines. Additionally, manoeuvrability may be compromised, particularly in larger vessels, posing safety concerns during docking or navigating narrow passages.
These performance inefficiencies quickly add up, forcing shipowners to balance the trade-offs between operational costs and proper maintenance routines.
Effects on Ship Longevity
Hull corrosion also affects the structural longevity of ships. A neglected hull can turn into a ticking time bomb, as weakened materials and delayed maintenance create long-term risks. Here's how corrosion compromises vessel lifespan:
Structural Weakening
Over time, corrosion can lead to material wastage, causing the thinning of steel hulls. This structural deterioration endangers the ship's integrity and increases the likelihood of cracks or fractures, especially when navigating harsh sea conditions.
Escalating Repair Costs
The deeper corrosion penetrates, the more complex and costly the repairs become. If protective coatings and preventive measures are neglected, repairs often involve intensive steel replacement or re-welding, which can significantly drive up costs.
Potential Safety Hazards
Neglecting corrosion can result in catastrophic consequences. Hull breaches may lead to flooding or complete structural failure. For tankers, corrosion could lead to oil spillage, resulting in environmental damage and hefty fines.
Thus, corrosion should not be overlooked as a minor maintenance issue; it can have far-reaching financial and safety repercussions if left unchecked.
Corrosion Prevention Methods
Given the high stakes, prioritising prevention is critical. Here are the top methods marine engineers and shipowners rely on to combat hull corrosion types effectively:
Advanced Coatings
Anti-corrosion coatings are the first line of defence against physical and chemical damage. Modern coating solutions, such as epoxy-based systems, offer excellent durability and resistance to microbial growth and galvanic corrosion. These coatings shield metal surfaces from direct contact with seawater and reduce fouling by repelling organisms.
Cathodic Protection Systems
Cathodic protection involves installing sacrificial anodes (typically zinc, aluminium, or magnesium) on the ship's hull to protect susceptible materials. By introducing a metal more reactive than the hull, the sacrificial anode corrodes while preserving the hull's structural steel.
Regular Inspections and Maintenance
Routine inspections using ultrasonic testing or visual methods help identify early signs of corrosion, enabling timely interventions. Hull cleaning schedules and spot repairs also play a key role in maintaining a ship's performance.
Submerged Hull Cleaning and Biofouling Treatments
Using advanced robotics or manual cleaning systems, biofouling can be safely removed, improving fuel efficiency and lowering drag. Eco-friendly anti-fouling paints further mitigate the risk of corrosion from trapped seawater.
Emerging Technologies
Technologies such as AI-assisted underwater drones are enabling more precise hull inspections. These drones use sensors and cameras to evaluate corrosion and fouling levels, making it easier to plan maintenance activities effectively.
Integrating these preventive measures into a ship's life cycle management is vital to ensuring sustainable operations.
Case Studies
To illustrate the severity and importance of corrosion management, here are real-world examples of its consequences and solutions:
The Cost of Neglect
A major shipping company operating bulk carriers faced significant operational downtime after severe hull corrosion went undetected. Structural thinning compromised the ship's integrity, requiring emergency dockyard repairs. Consequently, the company faced financial losses exceeding $2 million and reputation damage.
Effective Prevention Success Story
On the other hand, a fleet management firm that integrated advanced coatings and sacrificial anode systems into its routine maintenance schedule reported a 25% reduction in repair costs over five years. Regular inspections allowed for early interventions, keeping their fleet operational with minimal downtime.
These examples underscore the importance of proactive corrosion management for economic and operational efficiency.
Proactive Measures for Maximum Efficiency
Hull corrosion is more than a maintenance issue; it strikes at the heart of operational efficiency, safety, and sustainability in the maritime industry. Left untreated, it can significantly increase drag, escalate costs, and shorten a ship's lifespan.
Proactively managing hull corrosion through expert curation, coatings, and regular inspections ensures operational resilience and cost-efficiency while safeguarding the vessel's long-term health.
For marine engineers, naval architects, and shipowners, prioritising corrosion management isn't just a choice; it's a strategic necessity to thrive in the highly competitive maritime world. Stay ahead by integrating the latest technologies and maintenance strategies into your operations.
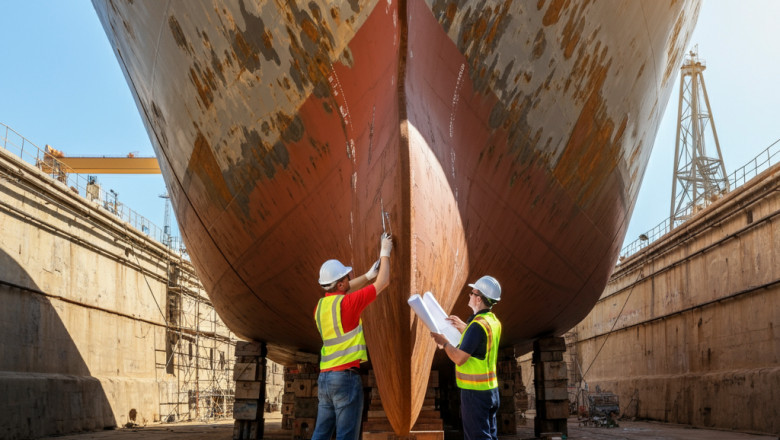

Comments
0 comment