How Injection Molding Machinery Is Powering Modern Manufacturing
In today’s fast-paced manufacturing world, where precision, efficiency, and innovation are key drivers, injection molding machinery plays a pivotal role. The versatility and capabilities of injection molding have made it the backbone of many industries, from automotive to electronics, medical devices, and consumer goods. This article explores how injection molding machinery has revolutionized manufacturing processes, contributing to higher productivity, lower costs, and greater design freedom.
The Basics of Injection Molding
Injection molding is a manufacturing process used to produce parts by injecting molten material into a mold cavity. These parts can be made from a variety of materials, including plastics, metals, and ceramics, with thermoplastics being the most common. The process begins with the raw material being heated until it reaches a liquid state. The material is then injected under high pressure into a mold, where it cools and solidifies into the desired shape. Once cooled, the part is ejected from the mold, and the cycle begins anew.
This highly automated process allows for mass production of complex parts with exceptional precision and consistency. The key to injection molding’s success lies in its ability to produce high volumes of parts quickly while maintaining tight tolerances, making it ideal for industries that demand high-performance, cost-effective solutions.
According to a Injection Molding Machinery Market report, the industry is expected to grow significantly in the coming years.
Speed and Efficiency: Meeting the Demands of Modern Manufacturing
One of the most significant advantages of injection molding machinery is its speed. The process can produce thousands of parts in a matter of hours, allowing manufacturers to meet high production demands without sacrificing quality. The cycle time for injection molding can range from a few seconds to several minutes, depending on the size and complexity of the part. However, modern injection molding machines are designed to minimize cycle times while maximizing output.
For industries such as automotive and electronics, where time-to-market is crucial, the efficiency of injection molding machinery is indispensable. Rapid prototyping, enabled by injection molding, allows manufacturers to test designs and iterate quickly, cutting down development time. This agility helps companies stay competitive in dynamic markets.
Additionally, the integration of advanced technologies, such as Industry 4.0 solutions, has further enhanced the speed and efficiency of injection molding. These technologies enable real-time monitoring, predictive maintenance, and automated adjustments to optimize machine performance and reduce downtime. By streamlining operations and increasing throughput, manufacturers can achieve higher productivity levels and lower production costs.
Precision and Consistency: Ensuring Quality Across Every Part
Injection molding is known for its ability to produce highly precise and consistent parts, which is essential for industries like medical devices and aerospace. Parts made through injection molding can achieve tight tolerances and intricate designs, ensuring that each unit meets the required specifications. This level of precision is achieved through the advanced control systems integrated into modern injection molding machines.
The consistency of injection molded parts is also a key benefit. Once the molding process is set up, it can run consistently with minimal human intervention, producing identical parts across multiple production runs. This consistency reduces the risk of defects, which is critical for industries where even small variations in part quality can have significant consequences.
For example, in the medical device industry, where the reliability and safety of components are paramount, injection molding allows manufacturers to produce parts that meet stringent regulatory requirements. Whether it's a small plastic component for a syringe or a more complex part for a surgical instrument, injection molding ensures that these parts are made to the highest standards, reducing the likelihood of defects and ensuring patient safety.
Design Flexibility: Enabling Complex Geometries
One of the most appealing aspects of injection molding is the freedom it provides designers in terms of part geometry. Unlike other manufacturing processes, injection molding allows for the production of highly complex shapes with intricate features such as undercuts, thin walls, and detailed textures. This capability opens up new possibilities for product design, giving manufacturers the flexibility to create parts that would be difficult or impossible to produce using other methods.
In addition to complex shapes, injection molding also enables the use of a wide range of materials. Thermoplastics, elastomers, and even metals can be molded to create components with different physical properties, such as flexibility, durability, or heat resistance. This versatility allows manufacturers to create parts that meet the specific requirements of their applications, whether it's a durable automotive component or a lightweight consumer product.
Furthermore, injection molding allows for the use of multi-material and multi-color molding. This process enables the production of parts that combine different materials or colors in a single cycle, offering even more design possibilities. For instance, automotive parts can be molded with both rigid and flexible components, improving functionality and reducing assembly time.
Sustainability: Reducing Waste and Energy Consumption
As sustainability becomes an increasingly important consideration in manufacturing, injection molding offers several advantages over traditional manufacturing methods. The process generates minimal waste, as the material is injected directly into the mold, and any excess material can be reused or recycled. In contrast to processes like machining or stamping, which can result in significant material waste, injection molding helps manufacturers minimize their environmental footprint.
Modern injection molding machines are also designed with energy efficiency in mind. Many machines feature energy-saving technologies, such as variable-speed drives and advanced heating systems, which help reduce power consumption during operation. Some machines also offer closed-loop systems that recycle the heat generated during the molding process, further improving energy efficiency.
Moreover, the ability to produce lightweight parts through injection molding contributes to sustainability efforts. Lighter parts require less energy to transport, reducing their carbon footprint over the product's lifecycle. The use of biodegradable or recyclable materials in injection molding also supports the growing demand for sustainable manufacturing practices.
Reducing Costs: Economical Mass Production
One of the primary reasons injection molding has become the preferred method for mass production is its cost-effectiveness. Once the initial mold is created, the cost per part decreases significantly as production volumes increase. This makes injection molding particularly advantageous for industries that require large quantities of components at a low cost per unit, such as the automotive, electronics, and consumer goods industries.
Although the upfront cost of creating a mold can be high, it is an investment that pays off over time due to the low per-part costs during mass production. This is particularly true for high-volume applications, where the cost of producing each part drops significantly as the production run increases. For manufacturers, this results in reduced overall production costs and improved profit margins.
Conclusion: The Future of Injection Molding in Modern Manufacturing
Injection molding machinery has evolved significantly over the years, enabling manufacturers to produce high-quality, cost-effective, and complex parts at unprecedented speeds. Its ability to deliver precision, design flexibility, and efficiency has made it an essential tool in modern manufacturing across a wide range of industries. With the continued advancement of automation, materials, and sustainability practices, the role of injection molding will only grow in importance.
As manufacturers seek to meet the demands of an increasingly globalized and competitive marketplace, injection molding machinery will continue to drive innovation, reduce production costs, and enable the creation of high-performance products that are shaping the future of manufacturing. Whether in the production of automotive components, medical devices, or consumer goods, injection molding will remain a cornerstone of modern manufacturing for years to come.
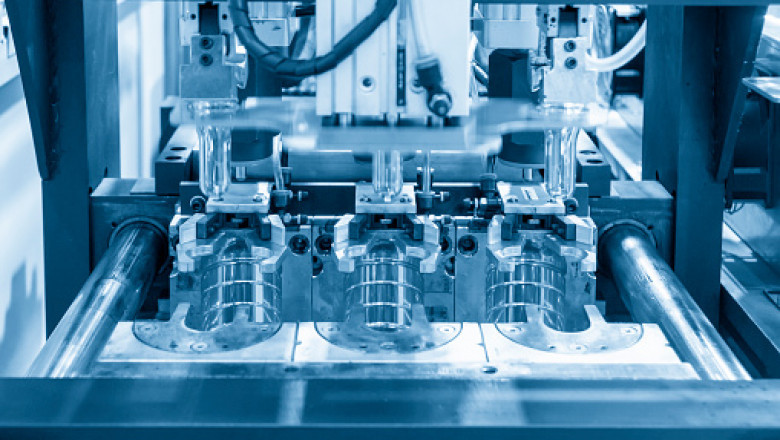

Comments
0 comment