views
Polyolefin shrink equipment plays a pivotal role in modern packaging, offering durability, versatility, and environmental benefits. Selecting the right machinery is crucial for optimizing packaging efficiency and product presentation. This guide delves into the essentials of polyolefin shrink equipment, assisting businesses in making informed decisions.
Understanding Polyolefin Shrink Film
Polyolefin shrink film is a polymer-based material renowned for its clarity, strength, and flexibility. When heat is applied, it conforms tightly to the product's shape, providing a secure and tamper-evident seal. Its attributes include durability against punctures and tears, making it ideal for various packaging needs. Moreover, polyolefin is environmentally friendly, often made from recyclable materials and free from chlorine, making it safe for food packaging.
Types of Polyolefin Shrink Films
There are two primary types of polyolefin shrink films: standard gauge and cross-linked.
Standard Gauge Polyolefin Shrink Film
This is commonly used for products that do not require significant additional protection. It is cost-effective and suitable for items like electronic goods, providing a protective layer against dust and minor abrasions during transit.
Cross-Linked Polyolefin Shrink Film
Through a chemical process involving high radiation exposure, cross-linked films have enhanced strength and durability. They are thinner yet maintain robustness, making them cost-effective. These films offer superior protection against chemicals and UV exposure, suitable for harsh environments. Applications include packaging perishable items like meat, ensuring hygiene and extending shelf life.
Essential Polyolefin Shrink Equipment
Selecting the appropriate equipment is vital for efficient packaging. The primary machines used in polyolefin shrink processes include:
L-Bar Sealers
L-Bar sealers are designed to create a seal around the product by cutting and sealing the shrink film in an "L" shape. They are available in manual, semi-automatic, and automatic configurations.
Semi-Automatic L-Bar Sealers
These machines require the operator to position the product and lower the sealing bar. Once sealed, the product is typically moved to a shrink tunnel for the film to conform tightly. Semi-automatic L-Bar sealers are suitable for medium-volume operations, offering a balance between manual labor and automation.
Automatic L-Bar Sealers
Ideal for high-volume packaging, these machines automate the sealing process, increasing efficiency and consistency. They can handle various product sizes and are often integrated with conveyors and shrink tunnels for streamlined operations.
Shrink Tunnels
Shrink tunnels apply consistent heat to the sealed product, causing the polyolefin film to shrink uniformly around the item. Features to consider when selecting a shrink tunnel include adjustable temperature controls, conveyor speed, and airflow, ensuring compatibility with different product sizes and film types.
Peripheral Equipment
To enhance the packaging process, peripheral equipment such as conveyors, feeders, and folders can be integrated. These components facilitate smooth product movement through the sealing and shrinking stages, reducing manual handling and increasing throughput.
Factors to Consider When Choosing Polyolefin Shrink Equipment
When selecting the appropriate shrink equipment, consider the following factors:
Production Volume
Determine your packaging needs based on daily or monthly output. Semi-automatic machines are suitable for medium volumes, while automatic systems are designed for high-volume operations.
Product Dimensions
Ensure the equipment can accommodate the size and shape of your products. Machines come with varying seal dimensions and tunnel sizes to handle different product specifications.
Film Compatibility
Verify that the equipment is compatible with the type and thickness of polyolefin shrink film you intend to use. Some machines are optimized for specific film gauges or formulations.
Budget Constraints
Balance initial investment costs with long-term operational efficiency. While automatic machines have higher upfront costs, they may offer cost savings through reduced labor over time.
Space Availability
Consider the physical footprint of the equipment and ensure your facility can accommodate it without disrupting workflow.
Maintenance and Support
Choose equipment from reputable manufacturers that offer reliable customer support and maintenance services to minimize downtime.
Advantages of Using Polyolefin Shrink Equipment
Investing in polyolefin shrink equipment offers several benefits:
Enhanced Product Protection
The shrink film provides a protective barrier against dust, moisture, and tampering, preserving product integrity.
Improved Aesthetics
Polyolefin film offers high clarity and gloss, enhancing product presentation and appeal.
Versatility
Suitable for a wide range of products, from food items to industrial goods, due to its adaptability and strength.
Environmental Considerations
Being recyclable and free from harmful chemicals, polyolefin shrink film aligns with sustainable packaging initiatives.
Cost-Effectiveness
The durability and efficiency of polyolefin shrink film can lead to reduced packaging material usage and lower transportation costs due to its lightweight nature.
Conclusion
Selecting the right polyolefin shrink equipment is crucial for achieving efficient and effective packaging solutions. Understanding the types of shrink films and machinery available, such as semi-automatic L-Bar sealers and the semi-automatic L sealer machine, enables businesses to tailor their packaging processes to specific needs. By considering factors like production volume, product dimensions, and budget, companies can invest in equipment that enhances product protection, presentation, and overall operational efficiency.
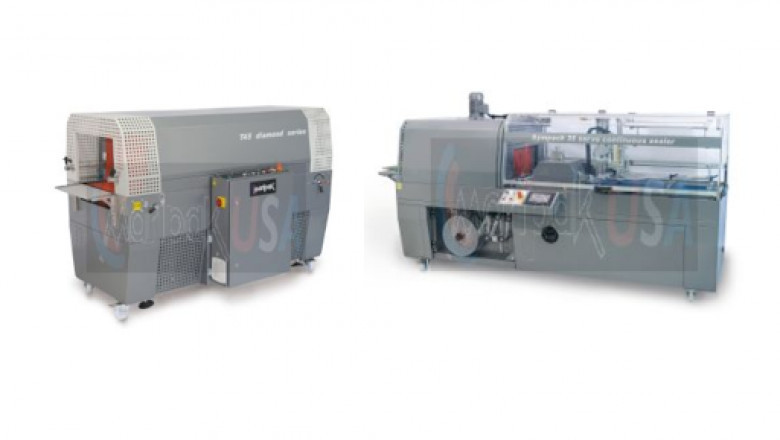

Comments
0 comment