views
Brass round bars represent a critical class of precision-engineered materials that combine metallurgical excellence with functional versatility. These cylindrical stock materials, produced to exacting Brass Round Bar ASTM and DIN standards, serve as fundamental components in high-performance mechanical systems, electrical infrastructure, and marine applications.
This engineering-focused guide examines:
-
Material science fundamentals of copper-zinc alloys
-
Standard specifications across global grading systems
-
Advanced mechanical properties and performance data
-
Precision machining considerations
-
Industry-specific application engineering
-
Technical procurement guidelines
Metallurgical Composition Analysis
Base Alloy Matrix
Element | Percentage Range | Functional Contribution |
---|---|---|
Copper (Cu) | 58-95% | Corrosion resistance, conductivity |
Zinc (Zn) | 5-42% | Strength enhancement, cost reduction |
Engineered Additives
Alloying Element | Technical Benefit | Commercial Grade Example |
---|---|---|
Lead (1-3%) | Chip-breaking during machining | C36000 (Free-cutting brass) |
Tin (0.5-2%) | Seawater corrosion resistance | C46400 (Naval brass) |
Aluminum (0.5-2%) | Oxide layer formation | C68700 (Aluminum brass) |
Manganese (0.5-3%) | Work hardening resistance | C67500 (Manganese brass) |
Mechanical Properties Database
Comparative Property Matrix
Property | C26000 (Cartridge) | C36000 (Free-cut) | C46400 (Naval) | C48500 (Leaded Naval) |
---|---|---|---|---|
Tensile (MPa) | 325-550 | 340-470 | 380-520 | 400-550 |
Yield (MPa) | 105-400 | 170-310 | 170-380 | 200-400 |
Elongation (%) | 55-15 | 50-18 | 50-15 | 45-12 |
Hardness (HB) | 60-155 | 80-135 | 85-150 | 90-160 |
Machinability (%) | 60 | 100 | 50 | 90 |
Note: Values vary with temper and processing
Precision Machining Technical Guidelines
Optimal Machining Parameters
Operation | Speed (SFM) | Feed (IPR) | Depth of Cut | Tool Material |
---|---|---|---|---|
Turning | 300-600 | 0.005-0.020 | 0.100-0.250 | Carbide/K10 |
Drilling | 150-300 | 0.003-0.010 | - | HSS-Co |
Milling | 250-500 | 0.002-0.015 | 0.050-0.150 | Carbide |
Threading | 100-200 | Pitch-dependent | - | HSS-E |
Surface Finish Considerations
-
As-drawn: 125-250 μin Ra
-
Turned: 32-125 μin Ra
-
Ground: 16-32 μin Ra
-
Polished: <16 μin Ra
Engineering Applications by Industry Sector
1. Power Generation Systems
-
Turbine governor components (C48500)
-
Bushing for hydroelectric plants (C86300)
2. Aerospace & Defense
-
Landing gear bushings (AMS 4610)
-
Radar waveguide components (C26000)
3. Medical Device Manufacturing
-
Surgical instrument fittings (C36000)
-
MRI component shielding (C22000)
4. High-Vacuum Systems
-
Particle accelerator components (C27200)
-
Semiconductor chamber fittings (C36000)
Technical Procurement Checklist
-
Material Certification
-
Mill test reports per ASTM B249
-
RoHS/REACH compliance documentation
-
-
Dimensional Tolerances
-
Diameter: ±0.001" (precision ground)
-
Straightness: 0.010"/ft max
-
-
Processing Requirements
-
Stress-relieved condition
-
Ultrasonic testing for critical applications
-
-
Packaging Specifications
-
VCI paper for corrosion protection
-
End caps for thread protection
-
Advanced Performance Testing Methods
Quality Verification Protocols
-
Metallography
-
Grain size analysis per ASTM E112
-
Phase distribution examination
-
-
Corrosion Testing
-
Salt spray (ASTM B117)
-
Stress corrosion cracking (ASTM G36)
-
-
Non-Destructive Evaluation
-
Eddy current testing
-
Ultrasonic thickness measurement
-
Conclusion: Engineering-Driven Material Selection
Brass round bars offer unparalleled design flexibility when properly specified for:
-
Fatigue resistance in dynamic applications
-
Galvanic compatibility in mixed-metal systems
-
Precision dimensional stability in machined components
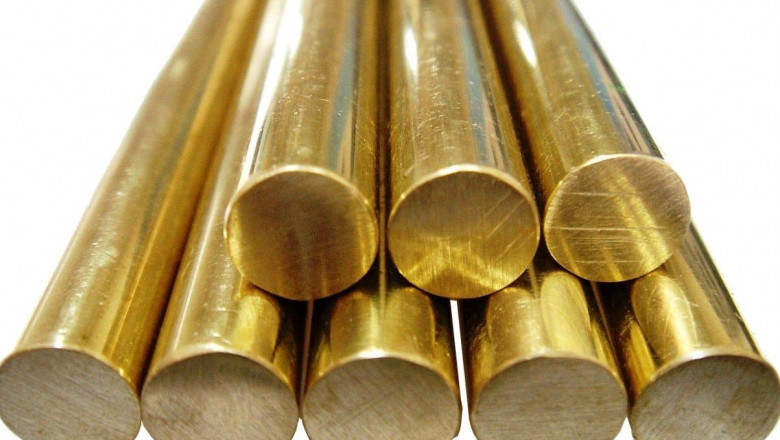

Comments
0 comment