views
When it comes to the world of industrial piping, ERW (Electric Resistance Welded) pipes have earned a significant place in applications across various industries. From construction to oil and gas pipelines, these pipes offer reliability, strength, and cost-effectiveness. This blog will guide you through everything you need to know about ERW pipes, including their manufacturing process, benefits, applications, and why they are a preferred choice in modern industries.
What is an ERW Pipe?
An ERW pipe is made through the Electric Resistance Welding process, where metal is welded using electric current. The process involves passing a current through metal, generating heat at the point of contact. This heat is then used to fuse the edges of the pipe together, forming a solid weld. The process creates a continuous pipe with a high-quality welded seam, which is why ERW pipes are highly regarded in the industrial sector.
Manufacturing Process of ERW Pipes
The manufacturing process of ERW pipes begins with cold-rolled or hot-rolled steel strips, which are cut to a predetermined width. These strips are then passed through a series of rollers that gradually form them into a cylindrical shape. The edges of the cylinder are then heated using electric current, which is directed through the metal at the point of contact. This generates heat sufficient enough to melt the edges and allow them to fuse together.
After welding, the pipe undergoes various stages of finishing. It is then cooled, cut into appropriate lengths, and tested for strength and durability. The pipes are also subjected to cleaning processes to ensure that any debris or impurities are removed before being sent for final inspection and packaging.
Types of ERW Pipes
ERW pipes can be divided into different types based on the applications they are designed for. These include:
-
Low-Carbon Steel ERW Pipes: Ideal for general-purpose applications, these pipes are often used in industries such as construction, water transportation, and HVAC systems.
-
High-Carbon Steel ERW Pipes: These pipes are stronger and more durable, making them ideal for high-pressure applications, such as in the oil and gas industry.
-
Galvanized ERW Pipes: These pipes are coated with a layer of zinc to protect them from corrosion. They are commonly used in applications exposed to harsh environments, such as agricultural and outdoor use.
-
Black ERW Pipes: These are the standard ERW pipes without any coating. They are used for applications where corrosion resistance is not a primary concern.
-
ERW Stainless Steel Pipes: Known for their corrosion resistance, these pipes are ideal for industries that require a high level of hygiene and durability, such as food processing and pharmaceuticals.
Advantages of ERW Pipes
-
Cost-Effectiveness: One of the main reasons industries prefer ERW pipes is their cost-effectiveness. The production process is highly efficient, which makes them cheaper to produce compared to other types of welded pipes, such as spiral-welded pipes.
-
Strength and Durability: ERW pipes are strong, durable, and resistant to internal and external stresses, making them a suitable option for high-pressure applications like oil and gas pipelines.
-
Corrosion Resistance: ERW pipes, especially the galvanized and stainless steel varieties, offer excellent resistance to corrosion, which is crucial for industries that operate in harsh environments.
-
Consistency in Quality: Since ERW pipes are produced through a controlled process, they tend to have consistent quality. The electric resistance welding process ensures uniformity in the weld, making them reliable for use in critical applications.
-
Wide Range of Sizes: ERW pipes are available in various diameters and thicknesses, allowing manufacturers and contractors to choose the right pipes based on their specific project requirements.
-
Ease of Welding: These pipes are easy to weld due to the quality of the welded seam, which results in fewer defects during the welding process and ensures the integrity of the piping system.
Applications of ERW Pipes
ERW pipes are used in a variety of industries due to their versatility. Some of the most common applications include:
-
Oil and Gas: ERW pipes are widely used in the oil and gas industry for transporting oil, gas, and other fluids. Their ability to withstand high pressure makes them ideal for pipelines.
-
Construction: In construction, ERW pipes are used for structural applications, such as in scaffolding, frames, and support systems.
-
Water Supply Systems: ERW pipes are commonly used for water transmission and distribution, owing to their durability and resistance to corrosion.
-
HVAC Systems: In heating, ventilation, and air conditioning (HVAC) systems, ERW pipes are used for piping installations, as they can handle both hot and cold water.
-
Automotive Industry: The automotive sector uses ERW pipes for exhaust systems, chassis, and other structural components.
-
Furniture and Handrails: ERW pipes are often used in the furniture industry for making durable, lightweight furniture and handrails due to their strength and easy weldability.
Factors to Consider When Choosing ERW Pipes
When selecting ERW pipes for a specific application, several factors should be considered:
-
Material: The material of the pipe should be chosen based on the type of fluid or gas that will pass through it. For example, stainless steel ERW pipes are suitable for corrosive substances, while carbon steel pipes are often used for general-purpose applications.
-
Size and Diameter: The size and diameter of the pipe must match the requirements of the application. Larger diameter pipes are used for transporting fluids over long distances, while smaller diameter pipes are ideal for systems that require more precise control.
-
Thickness: The thickness of the pipe wall is an essential factor in determining its strength and durability. Pipes with thicker walls are used in high-pressure systems, while thinner pipes are used in low-pressure applications.
-
Coating: Depending on the application, ERW pipes may be coated with materials such as zinc (galvanized) or other corrosion-resistant coatings to improve their longevity and performance in harsh environments.
Conclusion
ERW pipes are indispensable in various industries due to their strength, versatility, and cost-effectiveness. Whether you are in the construction, oil and gas, or automotive industry, ERW pipes offer a reliable and durable solution for your piping needs. With advancements in technology, the quality of ERW pipes continues to improve, ensuring that they remain the go-to choice for critical applications.
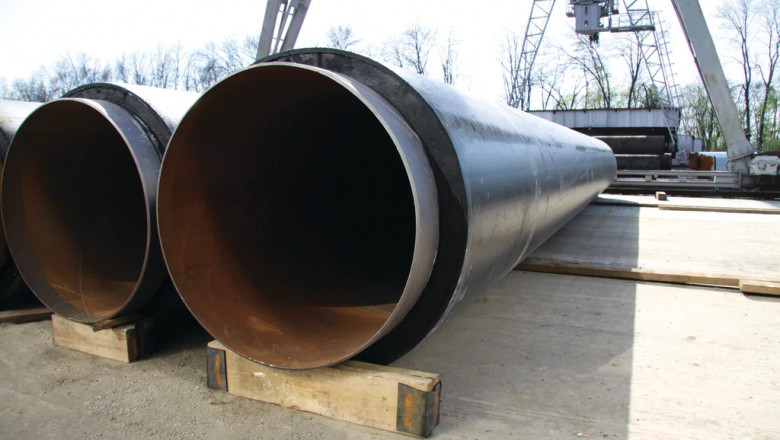

Comments
0 comment