views
This blog explains the different types of manifold valves—2-valve, 3-valve, and 5-valve—and their uses in various industries. It also highlights the importance of choosing the right **manifold valve manufacturer** for safe and efficient system operations.
Manifold valves are important tools used in many industries, especially where fluids or gases need to be controlled. These valves help in managing the flow, pressure, and direction of fluids in a system. A trusted manifold valve manufacturer designs these valves to meet different needs and working conditions.
In this blog, we will explain the different types of manifold valves and where they are used, in simple and easy words.
What Is a Manifold Valve?
A manifold valve is a device that connects multiple valves into one unit. It is used with pressure instruments like pressure gauges, transmitters, or switches. The main purpose of a manifold valve is to control the flow of liquids or gases, block or isolate pressure, and allow calibration or testing of instruments without removing them.
Common Types of Manifold Valves
There are several types of manifold valves, each designed for specific uses. Here are the most common ones:
1. 2-Valve Manifold
What It Does:
-
Has two valves: one for isolation and one for venting or pressure release.
-
Used to connect pressure gauges or pressure transmitters.
Application:
-
Best for simple pressure measurement setups.
-
Common in small piping systems and low-pressure applications.
2. 3-Valve Manifold
What It Does:
-
Includes three valves: one for high-pressure, one for low-pressure, and one equalizing valve.
-
Balances the pressure before removing or checking the instrument.
Application:
-
Often used with differential pressure transmitters.
-
Ideal for systems needing accurate flow or level measurement.
3. 5-Valve Manifold
What It Does:
-
Has five valves: two isolation valves, one equalizing valve, and two vent/drain valves.
-
Allows for safe calibration, testing, and venting.
Application:
-
Used in critical applications where precise and safe operations are needed.
-
Found in chemical plants, power plants, and oil & gas systems.
4. Remote Mounted and Direct Mounted Valves
-
Remote Mounted: Installed away from the instrument, connected with tubes or pipes.
-
Direct Mounted: Fitted directly on the instrument for better accuracy and space-saving.
Application:
-
Remote types are useful where the instrument cannot be placed near the valve.
-
Direct types are good for compact and easy setups.
Why Choosing the Right Manifold Valve Matters
Selecting the correct type of manifold valve depends on the system's need. A good manifold valve manufacturer provides options suitable for different pressure ratings, temperatures, and system types. Using the right valve improves safety, saves time, and increases the life of the instruments.
Final Thoughts
Manifold valves may look small, but they have a big role in many systems. Whether it's a 2-valve, 3-valve, or 5-valve design, each has a special job to do. With the help of a trusted manifold valve manufacturer, you can choose the right valve for your application and ensure smooth and safe operation of your system.
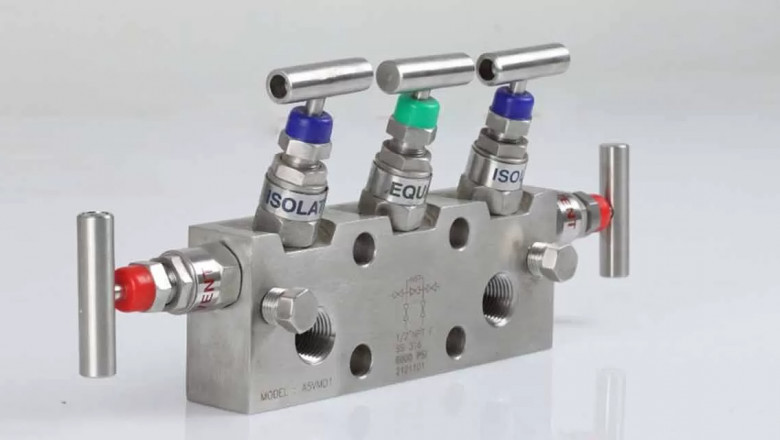

Comments
0 comment