views
Fasteners play a vital role in ensuring structural integrity and reliability across various industries. However, when exposed to harsh environments—like marine, offshore, or chemical processing—standard fasteners tend to fail due to corrosion, chemical attack, or thermal breakdown. That’s where PTFE coated fasteners come in.
Polytetrafluoroethylene (PTFE), commonly known by the brand name Teflon™, is a non-stick, corrosion-resistant material that significantly enhances the performance of metallic fasteners. These coated fasteners are gaining popularity due to their exceptional properties in demanding applications.
In this blog, we will explore the benefits, applications, specifications, and why PTFE coated fasteners are essential in modern industrial operations.
What Are PTFE Coated Fasteners?
PTFE coated fasteners are metal fasteners—such as bolts, nuts, washers, and screws—that are coated with a thin layer of PTFE. This layer acts as a protective shield that significantly improves the fastener’s resistance to corrosion, friction, and chemical degradation.
The coating process usually involves sandblasting the fastener surface, applying the PTFE coating evenly, and then curing it at high temperatures. The result is a smooth, durable surface that performs exceptionally well under extreme conditions.
Key Benefits of PTFE Coated Fasteners
1. Corrosion Resistance
One of the most important benefits of PTFE coating is its high resistance to corrosion. Whether in saltwater, chemical exposure, or industrial pollutants, PTFE coated fasteners resist rust and oxidation far better than uncoated alternatives.
2. Chemical Resistance
PTFE has excellent resistance to acids, bases, and solvents. This makes PTFE coated fasteners ideal for use in chemical processing plants and laboratories where exposure to aggressive substances is common.
3. Low Friction Coefficient
PTFE has one of the lowest coefficients of friction among solids. This characteristic allows easy installation and removal of fasteners, even after extended use in high-pressure environments. It reduces galling and seizing during tightening and loosening.
4. Thermal Stability
PTFE performs consistently in a wide temperature range—from -200°C to +260°C. This makes PTFE fasteners suitable for high-temperature applications like power plants and heat exchangers.
5. Non-Stick Surface
The non-stick nature of PTFE prevents dirt, debris, and chemicals from adhering to the fastener’s surface. This minimizes maintenance and ensures longer service life.
6. UV and Weather Resistance
PTFE does not degrade under UV rays or weather conditions. This is crucial for outdoor and marine applications where long-term exposure is expected.
Applications of PTFE Coated Fasteners
PTFE coated fasteners are extensively used in industries where reliability and longevity are non-negotiable. Here are a few sectors that benefit most from these high-performance fasteners:
● Oil & Gas Industry
Pipelines, drilling rigs, and offshore platforms require fasteners that resist salt spray, moisture, and chemicals. PTFE coated bolts and nuts are ideal for such conditions.
● Chemical Processing Plants
Fasteners used in chemical plants face constant exposure to harsh substances. PTFE coating ensures longevity and prevents breakdowns.
● Marine and Shipbuilding
Saltwater corrosion is a major concern in marine environments. PTFE coated fasteners offer excellent protection against rust.
● Food and Beverage Industry
Since PTFE is non-toxic and food-safe, coated fasteners are suitable for food processing equipment where hygiene is crucial.
● Power Generation
In thermal and nuclear power plants, high-temperature and high-pressure environments demand fasteners that can endure extreme stress.
● Water Treatment Facilities
PTFE coated fasteners withstand chlorine, acids, and other disinfectants used in water purification processes.
PTFE Coated Fasteners vs. Other Coatings
PTFE is not the only coating available, but it stands out due to its unique combination of properties. Here's how it compares:
Coating Type | Corrosion Resistance | Temperature Tolerance | Friction | Chemical Resistance |
---|---|---|---|---|
PTFE | Excellent | -200°C to +260°C | Very Low | Excellent |
Zinc | Moderate | Up to 120°C | Medium | Poor |
Hot-Dip Galvanized | Good | Up to 200°C | Medium | Moderate |
Epoxy | Good | Up to 150°C | Medium | Good |
As seen above, PTFE outperforms most standard coatings in multiple aspects.
Types of PTFE Coated Fasteners
Depending on the need, PTFE coating can be applied to a variety of fasteners. Some common types include:
-
PTFE coated bolts
-
PTFE coated nuts
-
PTFE coated washers
-
PTFE coated studs
-
PTFE coated screws
You can also request customized fasteners with specific thread patterns, sizes, and material combinations.
Considerations When Choosing PTFE Fasteners
When selecting PTFE coated fasteners, consider the following:
-
Substrate Material: Stainless steel, carbon steel, and Inconel are common base materials.
-
Coating Thickness: Typical PTFE coating thickness ranges from 20 to 40 microns.
-
Application Environment: Understand the temperature, pressure, and chemical exposure expected.
-
Certifications: Ensure the product meets relevant standards like ASTM, DIN, or ISO.
Why Source from a Trusted PTFE Fasteners Manufacturer?
Working with an experienced PTFE fasteners manufacturer in India ensures quality, customization, and timely delivery. Trusted manufacturers use advanced coating techniques, follow international standards, and provide documentation like Material Test Certificates (MTC), compliance sheets, and dimensional reports.
Additionally, reliable suppliers offer bulk availability, competitive pricing, and after-sales support—critical factors for large-scale industrial projects.
Final Thoughts
PTFE coated fasteners are a game-changer in industries where corrosion resistance, chemical stability, and thermal endurance are vital. Their superior properties ensure longer service life, reduced maintenance, and enhanced operational safety.
Whether you're managing a marine installation, a chemical plant, or a food processing facility, switching to PTFE coated bolts and nuts is a smart investment in reliability and performance.
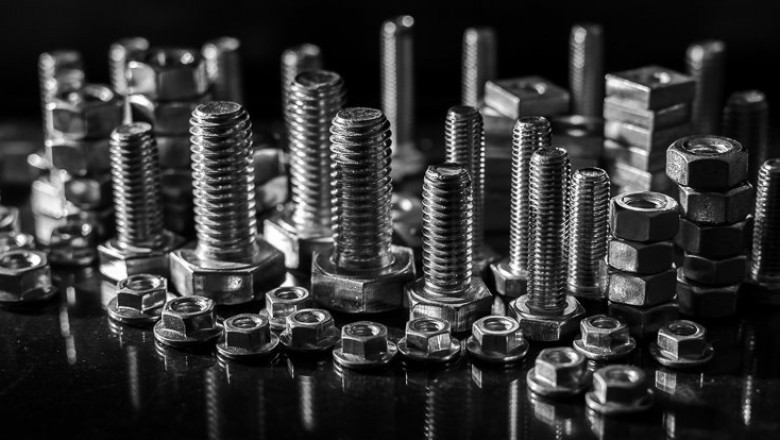

Comments
0 comment