views
Wet vs. Dry Vacuum Pumps: Pros and Cons Explained for Every Industry
Vacuum pumps are essential tools across a wide range of industries—from pharmaceuticals and food processing to electronics and chemical manufacturing. But with so many types available, one of the most important choices is between Wet vs. Dry Vacuum Pumps . Understanding the fundamental differences, advantages, and limitations of each can help you make an informed decision tailored to your application.
Understanding Vacuum Pumps
Vacuum pumps are mechanical devices designed to remove gas molecules from a sealed volume, creating a vacuum. These pumps vary in design, function, and application, but broadly fall into two categories: wet and dry vacuum pumps. The primary difference lies in how they handle lubrication and whether the working chamber comes into contact with fluids like oil or water.
What Are Wet Vacuum Pumps?
Wet vacuum pumps, also known as oil-sealed or liquid-ring vacuum pumps, use fluids such as oil or water within the compression chamber. These fluids act as both sealants and coolants, helping to achieve deeper vacuums and smoother operation.
Key Features of Wet Vacuum Pumps:
-
Use oil or liquid as a sealing and cooling medium
-
Often achieve higher ultimate vacuum levels than dry pumps
-
Handle high vapor loads well
-
Generally quieter in operation
-
Require regular maintenance for oil or liquid replacement
What Are Dry Vacuum Pumps?
Dry vacuum pumps operate without any oil or liquid in the compression zone. Instead, they rely on tight mechanical tolerances and innovative rotor designs—such as screw, scroll, or claw mechanisms—to compress and evacuate gases. They are known for their clean and oil-free operation.
Key Features of Dry Vacuum Pumps:
-
No contact between process gases and lubricants
-
Oil-free compression chamber
-
Minimal maintenance and servicing requirements
-
Ideal for applications that require contamination-free environments
-
Typically more energy-efficient over time
Advantages of Wet Vacuum Pumps
Wet pumps have long been the industry standard in many applications and bring several advantages:
-
High Vacuum Performance: Wet pumps can typically achieve deeper vacuum levels than dry pumps, especially in demanding applications.
-
Excellent Vapor Handling: The sealing fluid absorbs and condenses vapors, making wet pumps great for humid or wet processes.
-
Smooth Operation: The presence of fluid reduces wear and provides cushioning, which can make the operation quieter and more stable.
Disadvantages of Wet Vacuum Pumps
Despite their strengths, wet pumps come with notable limitations:
-
Contamination Risks: The oil or liquid can mix with process gases or vapors, leading to product contamination or hazardous waste.
-
High Maintenance Needs: Frequent oil changes and fluid monitoring are necessary to keep the system clean and functioning.
-
Environmental Concerns: Disposal of used oil or contaminated water can be costly and environmentally challenging.
-
Higher Operational Costs: Over time, oil replacements, filtration, and fluid handling can increase the total cost of ownership.
Advantages of Dry Vacuum Pumps
Dry pumps are increasingly favored for modern industrial setups thanks to their clean, efficient, and reliable operation:
-
Oil-Free and Contamination-Free: With no oil in the compression zone, there's no risk of product contamination—essential for cleanrooms and sensitive manufacturing processes.
-
Low Maintenance: Dry pumps require less frequent servicing, resulting in lower downtime and reduced long-term costs.
-
Environmentally Friendly: No need to dispose of contaminated fluids makes them a greener solution.
-
High Efficiency: Advanced designs often use less power and offer faster pump-down times for many applications.
Disadvantages of Dry Vacuum Pumps
While dry pumps offer several advantages, they are not without limitations:
-
Higher Initial Cost: The upfront investment in dry vacuum pumps is typically higher than that of wet pumps.
-
Sensitive to Particulates: Dry mechanisms can be more sensitive to dust and solid particles, which may require pre-filtration.
-
Limited Vapor Tolerance: Without a sealing liquid to absorb moisture, dry pumps may struggle in very wet or humid environments unless properly configured.
Side-by-Side Comparison of Wet and Dry Vacuum Pumps
Wet and dry vacuum pumps each serve different purposes depending on the specific demands of your process. Wet pumps may be better suited for high vapor loads or when a high vacuum is needed at a lower upfront cost. On the other hand, dry pumps shine in clean, low-maintenance environments where contamination control is crucial.
Factors to Consider When Choosing a Vacuum Pump
Selecting the right vacuum pump for your operation depends on a range of factors:
-
Type of Process Gas: If your application involves corrosive or condensable gases, you need a pump that can handle them safely—often a dry pump with proper coatings or a wet pump with compatible fluids.
-
Contamination Sensitivity: If cleanliness is a top priority (e.g., in pharmaceuticals or semiconductors), a dry vacuum pump is the better choice.
-
Vacuum Level Required: For deep vacuums, wet pumps might offer better performance. However, advances in dry technology are closing this gap.
-
Maintenance Resources: Consider how much time and cost you're willing to dedicate to regular maintenance. Dry pumps typically require less ongoing care.
-
Total Cost of Ownership: While dry pumps cost more upfront, they often provide better long-term savings due to reduced servicing and environmental costs.
-
Space and Noise Constraints: Wet pumps may be quieter, but modern dry pumps offer compact, modular designs with optional noise-reduction features.
In conclusion, both wet and dry vacuum pumps offer unique benefits and potential trade-offs. The best choice depends entirely on your operational needs, environmental concerns, and process requirements. Understanding the core differences between these two types of vacuum pumps empowers industries to make smart, efficient, and future-ready decisions.
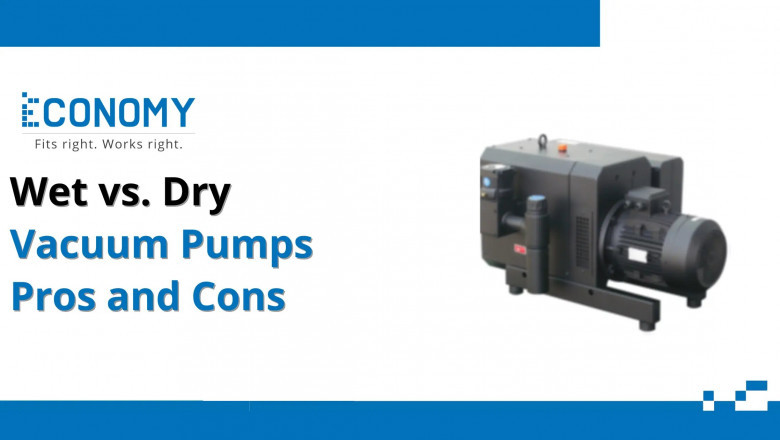

Comments
0 comment