views
What factors determine the efficiency of the horizontal ribbon mixer. - VORTEX Mixing Technology
The horizontal ribbon mixer is a widely used industrial machine, commonly employed in industries such as pharmaceuticals, food processing, chemicals, and construction materials for the blending of powders, granules, and other solid-based mixtures. Its core design features a U-shaped horizontal trough equipped with a central shaft bearing helical ribbons. These ribbons rotate to create a counter-flow motion within the material—moving product inward and outward, effectively blending the entire batch.
While the ribbon mixer appears simple in its mechanical function, its overall efficiency is determined by a complex interplay of factors, ranging from mechanical design elements to operational procedures and material characteristics. Each factor plays a significant role in influencing how thoroughly and quickly the mixer can achieve a homogenous blend, as well as how energy-efficient and cost-effective it can be during its operation.
One of the most critical factors affecting the efficiency of a horizontal ribbon mixer is the design of the agitator, particularly the geometry and pitch of the ribbon blades. The ribbons must be designed to ensure thorough movement of materials in both radial and axial directions. If the pitch is too tight, materials may not move freely and could create dead zones where blending is insufficient. Conversely, if the pitch is too open, the material may be pushed around with insufficient shear, resulting in a blend that is too gentle and possibly incomplete.
The clearance between the ribbon and the mixer trough wall is another essential aspect. Too large a clearance can lead to significant portions of material remaining unblended near the wall, while too tight a clearance may cause excessive friction, leading to heat generation, wear, and potential damage to heat-sensitive materials. Therefore, the design must strike a careful balance between shear, movement, and energy use, tailored to the physical properties of the materials being mixed.
The nature of the material being mixed significantly influences mixer efficiency as well. Bulk density, particle size distribution, flowability, and moisture content all impact how the ribbons interact with the material. For instance, fine powders may clump together due to electrostatic forces or moisture, requiring more vigorous mixing and potentially longer mixing times. Cohesive materials with high moisture content may stick to the ribbons or the trough, leading to uneven blending and difficult discharge.
On the other hand, free-flowing, uniform particles blend more quickly and uniformly, allowing for shorter mixing cycles. Additionally, when mixing materials with differing densities, achieving a uniform blend can be challenging, as heavier particles may tend to settle while lighter ones may float, requiring the mixer to run longer or be equipped with more aggressive mixing tools.
Understanding the physical characteristics of the mixture and customizing the mixer setup accordingly is vital for achieving maximum efficiency.
Operational parameters such as mixing time, rotational speed, and batch load size also play significant roles in determining the horizontal ribbon mixer’s efficiency. Mixing time is a delicate parameter; too short a duration may leave the blend incomplete, while too long can lead to material degradation, unnecessary energy expenditure, or even changes in material properties, especially for heat-sensitive or fragile ingredients. The rotational speed of the mixer is equally important.
While higher speeds can reduce mixing time, they may also lead to particle damage or create excessive heat. Furthermore, the batch size relative to the mixer’s capacity must be optimized. Underfilling the mixer reduces the contact between materials and the agitator, leading to poor mixing, while overfilling may overload the mixer, restrict material movement, and reduce mixing quality. Finding the optimal load and speed for each specific product type is often a result of careful testing and operational experience.
Another major factor that determines mixing efficiency is the condition and cleanliness of the mixer itself. Over time, product build-up on the ribbon blades or inside the trough can impede movement and lead to contamination between batches. Regular cleaning and maintenance are essential, especially in industries where cross-contamination can have serious consequences, such as pharmaceuticals and food production.
Additionally, wear and tear on the ribbons or seals can impact performance and lead to inefficiencies. For example, worn ribbons may lose their ability to generate the required shear and movement, while damaged seals may allow for product leakage or contamination. Preventive maintenance routines and stringent sanitation protocols help preserve the performance characteristics of the mixer and ensure it continues operating at peak efficiency over time.
Lastly, automation and process integration can further enhance the efficiency of horizontal ribbon mixers. Modern systems can be equipped with sensors and controls to monitor parameters such as load weight, torque, temperature, and mixing time in real-time. These systems can automatically adjust the mixer operation to optimize blending, improve consistency, and reduce operator error. Additionally, when ribbon mixers are integrated into larger automated production lines, the synchronization between mixing, feeding, and discharge processes can significantly reduce downtime, manual labor, and potential bottlenecks, leading to a more streamlined and efficient production process overall.
In summary, the efficiency of a horizontal ribbon mixer is the result of a multi-dimensional equation that includes mechanical design, material characteristics, operational parameters, maintenance protocols, and technological integration. Each of these factors must be carefully considered and optimized to ensure not only a homogenous and high-quality mix but also a cost-effective, safe, and reliable production process.
By understanding and managing these variables, operators and manufacturers can maximize the potential of their horizontal ribbon mixers and ensure consistent product quality across a wide range of applications.
Hot Search:Mixers
Conical Screw Mixer(Nauta Mixer)
Plough Shear Mixer
Twin Shaft Paddle Mixer
Ribbon Blender Mixer
Copyright © 2017- 2025 VORTEX Mixing Technology All Rights Reserved
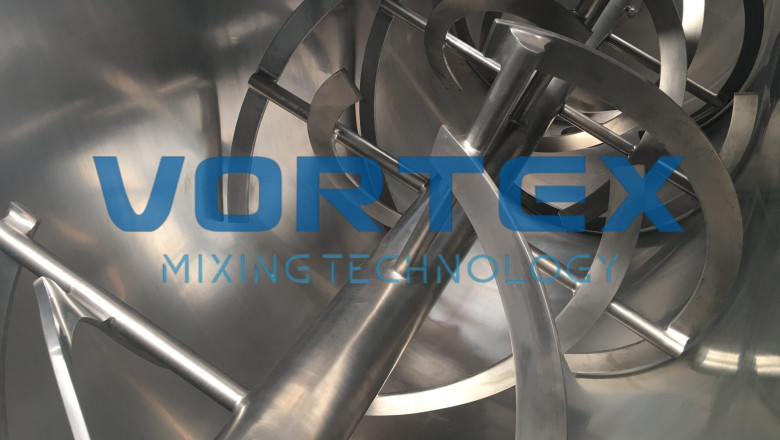

Comments
0 comment