views
Aluminum cable refers to electrical wiring made from aluminum conductors instead of traditional copper. While copper has long been the default for residential and commercial wiring, aluminum is gaining renewed attention due to its cost-efficiency, lightweight properties, and improved technology in alloys that make it safer and more reliable than before.
From residential buildings to industrial installations, aluminum cables are making a strong comeback—backed by innovations and compliance with modern electrical codes.
Key Benefits of Aluminum Cables
Feature | Aluminum Cable Advantages |
---|---|
Cost | 30–50% cheaper than copper wires |
Weight | About 50% lighter than copper |
Corrosion Resistance | Naturally forms an oxide layer for protection |
Flexibility | Easier to bend and route in large installations |
Availability | Readily available and scalable |
✅ Cost Efficiency Without Compromising Performance
Aluminum offers significant savings—especially in large-scale projects like:
-
Power distribution networks
-
Substations
-
Utility infrastructure
-
Renewable energy systems
You get more meters of cable per dollar spent, making it ideal for high-volume electrical needs.
✅ Lightweight and Installation-Friendly
Aluminum's lower density (2.7 g/cm³ vs. copper's 8.96 g/cm³) makes it ideal for:
-
Overhead power lines
-
Long-span applications
-
Easier handling during installation
-
Reduced structural load in buildings
This lightweight advantage translates to faster installs and reduced labor costs.
✅ Improved Alloys for Enhanced Safety
Modern AA-8000 series aluminum alloys address earlier concerns of creep and oxidation. These advanced materials meet NEC (National Electrical Code) standards for residential and commercial wiring.
Aluminum cables now include features such as:
-
Tinned or coated ends for oxidation resistance
-
Compression connectors to prevent loosening
-
Thermal-treated insulation to handle temperature variation
Where Is Aluminum Cable Commonly Used?
Aluminum cables are versatile. Their use spans across industries and applications:
-
Residential: Main service entrance wires, feeders
-
Commercial: Lighting circuits, HVAC systems
-
Utility/Power Distribution: Overhead transmission lines
-
Renewables: Solar PV systems, wind farms
-
Industrial: Machinery, control panels, switchboards
Is Aluminum Wiring Safe?
This question comes up often. The short answer: Yes—when installed properly with approved materials and methods.
In the 1960s–70s, aluminum wiring gained a bad reputation due to improper installations and incompatible devices. But those issues stemmed from old aluminum grades (1350) and poor connections—not the metal itself.
Today, certified aluminum wiring systems use:
-
Anti-oxidant compounds
-
Torque-tested lugs
-
AL-compatible switches and outlets
With proper terminations and maintenance, aluminum cable systems are UL-Listed and meet IEC/NEC/CSA standards.
Aluminum Cable vs. Copper Cable – What's the Difference?
Feature | Aluminum Cable | Copper Cable |
---|---|---|
Conductivity | ~61% of copper | 100% |
Cost | 30–50% less expensive | More expensive |
Weight | Lighter (50% lighter) | Heavier |
Thermal Expansion | Higher (needs flexible connectors) | Lower (more stable under heat) |
Installation | Easier for long distances | More compact in tight spaces |
Corrosion | Oxidizes but self-seals | More resistant in general |
While copper has a higher current-carrying capacity, aluminum compensates with larger gauge sizes at lower cost. When designed correctly, aluminum systems offer comparable performance.
FAQs About Aluminum Cable
🔹 Can I use aluminum cable in my house?
Yes—especially for main feeder lines, subpanels, or larger circuits like air conditioners and ovens. Just ensure:
-
Connectors are rated for aluminum (AL/CU)
-
Anti-oxidant paste is applied
-
Proper torque specs are followed
🔹 Does aluminum wire overheat?
Not inherently. Overheating occurs only if connections are loose or corroded. Proper torque settings, using compression terminals, and regular inspection prevent this.
🔹 Is aluminum cable compatible with copper?
Direct contact between aluminum and copper is not recommended due to galvanic corrosion. Use a bimetallic connector or approved transition splice kits for safe connections.
🔹 How long does aluminum cable last?
Aluminum conductors have a lifespan of 40–50 years, depending on:
-
Environmental exposure
-
Quality of installation
-
Insulation materials
In fact, many overhead transmission lines using aluminum have been in service for over half a century.
🔹 Which cable is better for solar installations—aluminum or copper?
Aluminum cables are ideal for solar farms due to their:
-
Long runs from panels to inverters
-
Cost advantages for high-volume use
-
Compatibility with aluminum-rated terminals in modern inverters
Copper may still be preferred in tight-space rooftop solar systems, but for ground-mounted PV arrays, aluminum wins in cost-to-performance ratio.
Common Types of Aluminum Cables
Type | Description | Application |
---|---|---|
AAC (All Aluminum Conductor) | Lightweight, high conductivity | Urban overhead power lines |
AAAC (All Aluminum Alloy Conductor) | Enhanced strength, corrosion resistance | Coastal/industrial power systems |
ACSR (Aluminum Conductor Steel Reinforced) | Steel core, high tensile strength | Long-distance transmission lines |
ACWU90 / TECK90 | Armored, insulated for direct burial | Commercial & industrial installations |
SER / SEU | Service entrance cable | Residential feeder applications |
Installation Tips: How to Safely Work With Aluminum Cables
Installer expertise is critical. Follow these best practices to ensure safety and performance:
-
Always use AL-rated terminals or connectors
-
Apply anti-oxidant paste on exposed ends
-
Torque connections to manufacturer specifications
-
Periodically inspect junctions and panels
-
Avoid excessive bending or over-tightening
-
Use compression lugs where possible
Correct tools and materials prevent common issues like oxidation, thermal expansion loosening, or electrical resistance at joints.
Industry Standards and Certifications
To ensure safety and compliance, aluminum cable must follow regulations such as:
-
UL 44, UL 854 – Safety of power and service entrance cables
-
NEC Article 310 – Wiring methods and materials
-
ASTM B800 / B801 – Mechanical and electrical performance
-
CSA C22.2 / IEC 60228 – Global electrical conductor standards
These certifications ensure that aluminum cables are designed for durability, conductivity, and fire resistance.
Who Uses Aluminum Cables?
Major industries that use aluminum wiring include:
-
Energy and Utilities: Long-distance high-voltage transmission
-
Construction: Multi-family and commercial buildings
-
Transportation: Rail and airports require lightweight wiring
-
Manufacturing Plants: Electrical panels, motors, control wiring
-
Data Centers: Efficient power delivery with reduced cable weight
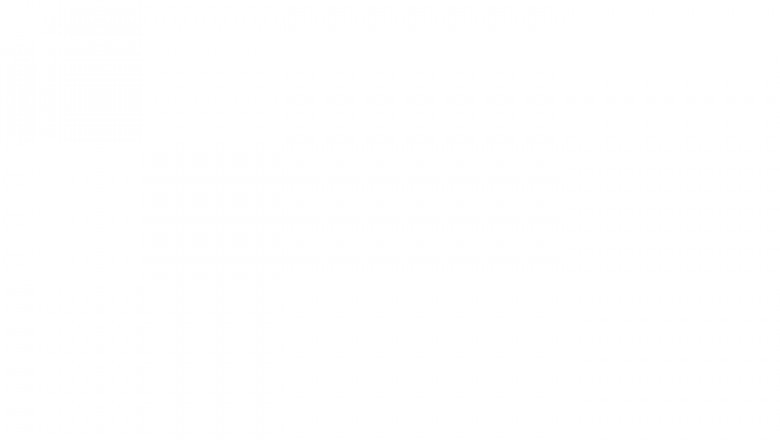

Comments
0 comment