views
Introduction to FEA Engineering
In today’s competitive engineering landscape, innovation, speed, and precision are more important than ever. To meet these demands, industries across automotive, aerospace, electronics, construction, and more are turning to simulation-based solutions to optimize design and performance. One of the most transformative tools in this domain is Finite Element Analysis (FEA).
FEA engineering enables engineers to analyze how a product will react to real-world forces, such as vibration, heat, fluid flow, and other physical effects. This digital simulation technique saves time, reduces costs, and improves the safety and reliability of products—making it a cornerstone of modern engineering.
What is FEA Engineering?
Finite Element Analysis (FEA) is a computerized method used to predict how a product reacts to real-world forces. It breaks down a complex object into smaller elements and applies equations to simulate behavior under various conditions. These elements form a mesh, and by solving equations for each element, engineers can get an accurate picture of how the entire object will perform.
FEA is particularly useful in structural analysis, where it helps determine stress points, potential failures, and areas that may need reinforcement or redesign. However, its use extends beyond just structural analysis; FEA is also critical in thermal analysis, electromagnetic simulations, and fluid-structure interactions.
Applications of FEA Engineering
1. Product Design and Optimization:
FEA allows engineers to test multiple design iterations without having to build physical prototypes. This makes the product development process faster and more cost-effective. It helps in reducing material usage while maintaining structural integrity.
2. Structural Integrity and Safety:
In sectors like aerospace and automotive, ensuring structural integrity is essential. FEA helps predict how a structure will behave under various loads, preventing costly failures and increasing safety.
3. Thermal Management:
In electronics and manufacturing, thermal management is a major concern. FEA simulations help analyze how heat is distributed and identify hot spots or areas needing cooling improvements.
4. Fluid-Structure Interaction:
When a structure interacts with fluids (like air or water), the combined behavior can be complex. FEA tools, often used in conjunction with computational fluid dynamics consulting, allow engineers to study this interaction and optimize designs accordingly.
The Role of Computational Fluid Dynamics Consulting
While FEA focuses on structural and thermal analysis, computational fluid dynamics (CFD) deals with fluid behavior and how fluids interact with surfaces. Computational fluid dynamics consulting services are often employed alongside FEA to provide a complete simulation package.
CFD consulting firms bring specialized expertise in simulating airflow, liquid behavior, and heat transfer through fluids. This is particularly beneficial in industries like HVAC, aerospace, marine, and automotive, where fluid dynamics significantly impact performance and efficiency.
By integrating CFD with FEA, engineers can perform multiphysics simulations that consider both solid and fluid domains. For example, simulating how airflow over a car hood affects the structural integrity of components beneath it requires both FEA and CFD expertise.
Software Tools Used in FEA Engineering
A wide range of software tools support FEA simulations, including:
-
ANSYS: One of the most widely used platforms for structural, thermal, and fluid simulations.
-
Abaqus: Ideal for complex material modeling and nonlinear simulations.
-
SolidWorks Simulation: Popular in mechanical design and prototyping.
-
COMSOL Multiphysics: Known for its multiphysics capabilities, integrating structural, thermal, and fluid interactions.
These tools help engineers visualize stress distributions, deformation patterns, temperature gradients, and more—guiding better design decisions.
Benefits of FEA Engineering
-
Cost Reduction: Identifying potential failures early reduces the need for expensive rework or recalls.
-
Time Efficiency: Design cycles are shortened as fewer physical prototypes are needed.
-
Improved Performance: Optimized designs result in better product performance and reliability.
-
Enhanced Safety: Predicting failure modes allows engineers to reinforce weak areas before manufacturing.
-
Sustainability: Efficient use of materials and energy leads to more eco-friendly designs.
Conclusion
FEA engineering has transformed the way products are designed, tested, and refined. By allowing for virtual simulations of real-world scenarios, it empowers engineers to make smarter, faster, and safer design decisions. When paired with computational fluid dynamics consulting, companies can leverage a full spectrum of simulation capabilities to innovate and outperform the competition.
As industries continue to push the boundaries of design and functionality, the role of FEA and CFD in product development will only grow more vital. Investing in these technologies and services is no longer optional—it’s a strategic necessity.
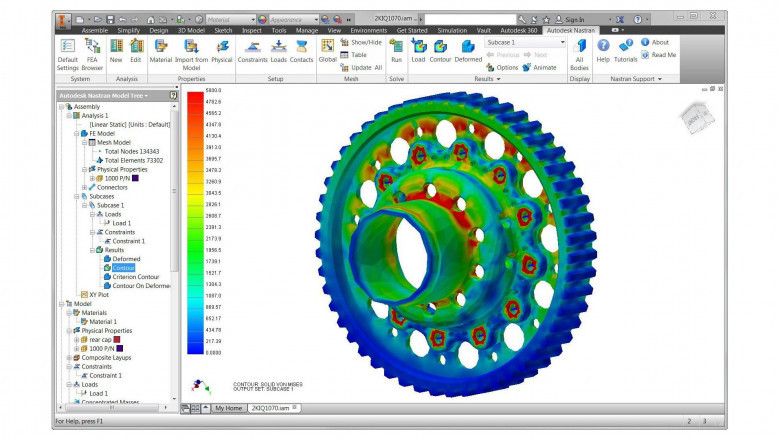

Comments
0 comment