views
The pharmaceutical industry is witnessing a paradigm shift in the manufacturing processes of Generic Active Pharmaceutical Ingredients (APIs), driven by the need for increased efficiency, sustainability, and product quality.
1. Optimization of Synthetic Pathways
One of the primary avenues for improvement lies in the optimization of synthetic pathways. Researchers strive to refine multi-step synthesis processes by minimizing the generation of intermediate products and streamlining purification techniques. This not only enhances the overall yield but also reduces time and resource consumption. The exploration of novel catalysts and reaction conditions has made the synthesis of complex molecules significantly more efficient. Additionally, the adoption of green chemistry principles has come to the forefront, emphasizing the reduction of hazardous solvents and promoting resource efficiency. For instance, using water as a solvent and sourcing renewable materials significantly decreases environmental impact.
2. Automation and Creative Manufacturing
The integration of automation and creative manufacturing technologies is revolutionizing API production lines. Advanced automation techniques facilitate the comprehensive monitoring and adjustment of manufacturing processes, thereby enhancing productivity and ensuring product consistency. Furthermore, the application of data analytics and machine learning algorithms aids in optimizing parameters within the manufacturing process. This proactive approach minimizes human error, leading to improved yields and significant operational efficiencies.
3. Small-Scale Production Facilities
As market demand continues to evolve, the development of small-scale, modular production facilities has gained popularity. These facilities allow for rapid responses to varying market needs, particularly for high-value patented drugs or emerging pharmaceuticals. This flexibility not only shortens time-to-market but also reduces production costs, enabling companies to adapt swiftly to new drug developments and changing consumer demands.
4. Continuous Flow Reaction Technology
The implementation of continuous flow reactors represents a significant advancement in chemical reaction processes. This technology enables efficient chemical transformations while enhancing safety and control over complex reaction conditions. Continuous flow methods allow reactions to occur at precisely regulated temperatures and pressures, which boosts reaction efficiency and selectivity. This approach has proven particularly advantageous for sensitive reactions and unstable intermediates, significantly mitigating risks associated with batch-based processes.
5. Quality Control and Assurance
Enhanced quality control measures are crucial for ensuring API efficacy. The integration of online detection and Process Analytical Technology (PAT) enables real-time monitoring of key quality attributes throughout production. This ensures compliance with established standards at every stage of the production process, minimizing the risk of non-conforming end products. Additionally, implementing rigorous quality management systems, such as Six Sigma, leads to reduced variability in production and improved product consistency.
6. Collaboration and Knowledge Sharing
Finally, the growing collaboration among pharmaceutical companies, academia, and governmental entities is critical for fostering technological innovation. Multidisciplinary research teams that combine expertise from chemistry, materials science, and data science drive the advancement of manufacturing processes, accelerating improvements in API production.
These advancements not only enhance the efficiency of API production but also lower costs, improve product quality, and ensure safety. Ultimately, these innovations are vital for meeting the evolving demands of the market and advancing the development of generic and biosimilar pharmaceuticals. The future of API manufacturing is poised for remarkable progress, underpinned by technological advancements and a commitment to sustainability.
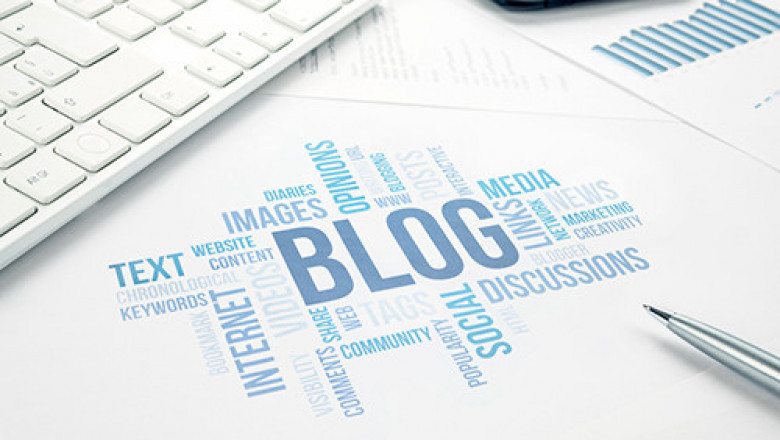

Comments
0 comment