views
significant role in determining the overall efficiency of the turbine engine, affecting power output and operational stability. Without an effective compression process, the engine would struggle to generate sufficient thrust or power. This blog explores the types of compressors used in turbine engines, their key components, their functions, and the latest advancements in compressor technology.
Types of Compressors in Turbine Engines
Centrifugal Compressors
Centrifugal compressors use a rotating impeller to accelerate incoming air outward, increasing its pressure through centrifugal force. These compressors are commonly found in smaller gas turbines and turbochargers due to their simple design, compact size, and high-pressure ratios per stage. However, they are less efficient for larger engines that require continuous airflow compression.
Axial-Flow Compressors
Axial-flow compressors consist of multiple rows of rotor and stator blades arranged in sequence to progressively increase the air pressure. These compressors are used in large jet engines and industrial gas turbines due to their ability to handle high airflow rates and deliver consistent compression over multiple stages. They are more complex and expensive than centrifugal compressors but provide higher efficiency and performance.
Comparison of Compressor Types
Centrifugal compressors are simpler and suitable for smaller engines, while axial-flow compressors are preferred for high-performance applications such as aviation and power generation. The choice between the two depends on factors like size constraints, efficiency requirements, and pressure ratio needs.
Main Components of a Compressor and Their Functions
Inlet Guide Vanes (IGVs)
Inlet guide vanes are positioned at the entrance of the compressor and help regulate the flow of air into the compression stages. They adjust the angle of incoming air to optimize aerodynamic efficiency, reducing the risk of compressor stalls and surges. Some modern engines use variable guide vanes that adjust dynamically based on engine conditions.
Rotor Blades
Rotor blades are rotating airfoils that accelerate incoming air and increase its velocity. As the air moves through the rotating blades, its kinetic energy rises, which is later converted into pressure. The shape and material composition of rotor blades play a crucial role in compressor efficiency and durability.
Stator Blades
Stator blades are stationary components located between the rotor blades. Their primary function is to diffuse high-velocity air, slowing it down and converting kinetic energy into pressure. This alternating rotor-stator arrangement allows the compressor to gradually increase air pressure across multiple stages.
Diffuser
The diffuser is a critical part of the final compression stage. It slows down the airflow coming from the stator blades, allowing the pressure to rise further before the air enters the combustion chamber. This controlled pressure increase ensures optimal fuel-air mixing and combustion efficiency.
Operational Mechanism of the Compressor
Air Intake and Initial Compression
The process begins when air enters the compressor through the inlet guide vanes, which regulate airflow and prevent turbulence. The rotor blades then accelerate the air, increasing its velocity while maintaining a steady flow.
Sequential Compression Stages
As the air moves through each stage of the axial-flow compressor, it alternates between rotor and stator blades. The rotor blades increase air velocity, while the stator blades convert velocity into pressure. This stepwise compression process allows for a gradual and controlled pressure increase without excessive temperature rise.
Temperature and Pressure Increase Through the Compressor
With each stage, the pressure and temperature of the air rise significantly. By the time the compressed air reaches the diffuser, it has achieved the desired pressure level required for efficient combustion. The balance between temperature and pressure is crucial, as excessive heat can reduce efficiency and damage components.
Common Issues and Maintenance of Compressors
Compressor Stall and Surge
A compressor stall occurs when airflow within the compressor becomes disrupted, leading to airflow separation and loss of pressure. This can cause engine instability and even failure. A compressor surge is a more severe condition where airflow momentarily reverses, causing violent pressure fluctuations and potential engine shutdown. Regular maintenance and proper airflow management help prevent these issues.
Blade Erosion and Fouling
Over time, compressor blades suffer from erosion and fouling due to exposure to dust, debris, and high-velocity air. Blade erosion reduces aerodynamic efficiency, while fouling (buildup of contaminants) affects airflow patterns. Cleaning techniques such as water washing and chemical cleaning help restore blade performance.
Inspection and Maintenance Practices
Routine inspection using non-destructive testing (NDT) methods, such as ultrasonic or borescope inspections, helps detect early signs of blade wear, cracks, or misalignment. Scheduled maintenance and timely blade replacements ensure consistent engine performance and reliability.
Gas Turbine Control System: Optimizing Compressor Performance
The gas turbine control system plays a crucial role in regulating the operation of the compressor, ensuring efficient airflow management and stable turbine performance. By continuously monitoring and adjusting key parameters, the control system helps prevent issues such as compressor surge, stall, and excessive wear on components.
Key Functions of the Gas Turbine Control System in Compressor Operation
Airflow Regulation and Pressure Control
The control system optimizes the compressor’s airflow by adjusting variable inlet guide vanes (VIGVs) and stator vanes.
It maintains the right pressure ratios to ensure smooth compression without causing excessive thermal stress.
Prevention of Compressor Surge and Stall
By monitoring pressure fluctuations, the control system detects early signs of surge and takes corrective actions, such as adjusting fuel flow or modulating guide vanes.
It ensures stable operation by balancing the relationship between compressor speed and airflow demand.
Fuel and Combustion Optimization
The system synchronizes compressor performance with fuel injection rates to maintain efficient combustion.
This prevents overheating, reducing strain on compressor blades and casing.
Temperature and Vibration Monitoring
Sensors track temperature variations across compressor stages, preventing thermal expansion-related failures.
Vibration analysis helps identify early signs of wear or imbalance, triggering maintenance alerts before major breakdowns occur.
Integrated Diagnostics and Predictive Maintenance
Advanced GE and other gas turbine control systems use AI-driven analytics to predict compressor part failures before they occur.
This enhances reliability, reduces downtime, and extends the life of critical compressor components.
GE's Gas Turbine Control System is designed to optimize performance, enhance reliability, and ensure precise monitoring of key parameters such as fuel flow, temperature, and pressure, enabling efficient and safe turbine operation. IS215UCVEM06A, IS200TSVOH1BBB are examples of GE gas turbine control system components.
Conclusion
The compressor is a vital component of a turbine engine, responsible for increasing air pressure and ensuring efficient combustion. Various parts, such as inlet guide vanes, rotor and stator blades, diffusers, and casings, work together to achieve optimal compression and engine performance. Regular maintenance, advanced blade designs, and emerging technologies contribute to enhancing compressor efficiency and longevity. As gas turbine technology continues to evolve, compressors will become even more efficient, reliable, and adaptive to modern energy and aviation demands.
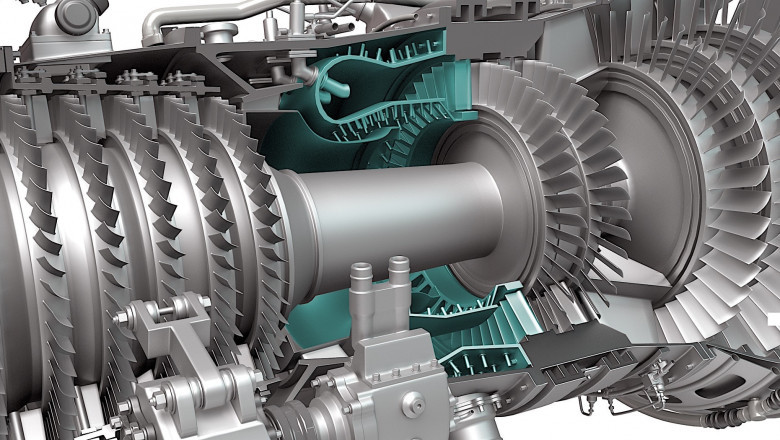

Comments
0 comment