views
In the construction industry, managing inventory efficiently is crucial for maintaining project timelines, controlling costs, and ensuring smooth operations. With vast amounts of materials, tools, and equipment on-site, traditional methods of tracking inventory are no longer sufficient.
Best software for construction inventory management comes into play. These modern software solutions enable construction companies to streamline their inventory processes, reduce waste, and prevent costly delays, ultimately boosting productivity and profitability.
The Challenges of Construction Inventory Management
Construction inventory management involves keeping track of numerous assets and materials, ranging from raw materials like concrete and steel to specialized equipment and tools. Managing this large volume of inventory manually is both time-consuming and prone to errors. Without a proper system in place, construction companies can face a variety of challenges, including:
-
Over-purchasing materials, which leads to excess stock and increased storage costs.
-
Under-purchasing materials, resulting in delays when materials run out mid-project.
-
Lost or misplaced tools and equipment, which can lead to wasted time and lost productivity.
-
Inaccurate inventory records, making it difficult to plan future projects and make informed purchasing decisions.
According to a survey by the National Association of Home Builders, 35% of construction companies report that poor inventory management results in project delays. To avoid these problems, the industry is increasingly turning to software for construction inventory management to improve accuracy and efficiency in inventory tracking.
How Software Solutions Optimize Construction Inventory Management
1. Real-Time Inventory Tracking
One of the most significant advantages of the software for construction inventory management is its ability to provide real-time tracking of inventory. Whether it's tools, materials, or equipment, these software solutions enable project managers to see the current stock levels and location of every item in the inventory.
Real-time tracking not only reduces the chances of losing track of materials but also allows project managers to make quick decisions when inventory levels are low. For example, if a certain material is running low on-site, the software can automatically alert the manager, ensuring timely reordering and avoiding project delays. This feature also helps construction companies keep their inventory lean, ensuring they only purchase what they need when they need it.
2. Automated Replenishment and Ordering
With the best software for construction inventory management, companies can automate the process of replenishing stock, reducing the likelihood of both over-ordering and under-ordering. These systems are equipped with inventory thresholds that automatically trigger reordering when stock falls below a set level.
For example, if a construction company is working on a project that requires large quantities of lumber, the software can monitor inventory levels and automatically place an order with the supplier once it reaches a predetermined minimum threshold. This automated process eliminates the guesswork from inventory management, saving both time and money while ensuring materials are always available when needed.
3. Barcode and RFID Scanning
Barcode and RFID scanning capabilities are built into many of the software for construction inventory management solutions. With this technology, construction companies can easily track and manage the movement of materials, tools, and equipment across job sites.
Instead of manually entering inventory data into a spreadsheet or system, construction workers can scan barcodes or RFID tags on items as they are moved, used, or returned to the warehouse. This significantly reduces human error and ensures that inventory records are always up to date. Additionally, the software can provide detailed reports on the usage of materials, allowing managers to track waste and identify potential areas for cost savings.
4. Centralized Inventory Data and Integration
The software for construction inventory management provides a centralized platform where all inventory data is stored and accessible from anywhere. This centralized system allows project managers, procurement teams, and other stakeholders to access up-to-date information on materials and equipment in real time, ensuring everyone is on the same page.
Moreover, modern inventory management software integrates seamlessly with other construction management tools, such as project scheduling, budgeting, and procurement systems. This integration allows for better coordination between teams, streamlining workflows and improving overall project efficiency.
5. Advanced Analytics and Reporting
Advanced analytics and reporting features in modern inventory management software offer construction companies valuable insights into their inventory practices. By analyzing data on material usage, procurement trends, and inventory turnover, these software solutions can help companies identify inefficiencies and optimize their inventory strategies.
For example, detailed reports on material consumption can help construction companies identify which materials are being used most frequently, allowing them to better forecast future inventory needs and avoid overstocking or stockouts. Additionally, reports on supplier performance can help companies make more informed decisions when selecting suppliers, ensuring that they are getting the best deals and service.
The Benefits of Optimizing Construction Inventory with Software Solutions
1. Cost Savings
By using the construction inventory management, construction companies can save money in several ways. First, real-time tracking and automated replenishment help avoid overstocking, reducing unnecessary storage costs. Second, optimized inventory levels reduce the risk of under-ordering materials, which can lead to project delays and increased procurement costs. Finally, accurate tracking of materials helps minimize waste, leading to further savings on materials and resources.
2. Improved Efficiency and Productivity
Inventory optimization software streamlines workflows by automating manual tasks such as stock counting, ordering, and reporting. This frees up employees to focus on more value-added activities, increasing overall productivity. Additionally, accurate inventory data ensures that construction teams always have the right materials at the right time, preventing delays and downtime due to missing items.
3. Better Project Management
By providing real-time data on inventory levels, usage, and costs,construction inventory management enables project managers to make more informed decisions. Accurate inventory data helps with budgeting, scheduling, and forecasting, ensuring that construction projects stay on track and within budget. With better control over materials and resources, project managers can also prevent delays and minimize risks.
Conclusion
In conclusion, optimizing construction inventory with Best software for construction inventory management is no longer optional; it's essential for improving efficiency, reducing costs, and ensuring the success of construction projects. By providing real-time tracking, automating reordering, integrating with other systems, and offering detailed analytics, modern software solutions help construction companies take control of their inventory and streamline operations.
As the construction industry continues to embrace digital transformation, investing in modern inventory management software is a smart decision for any company looking to stay competitive and achieve greater profitability. With these tools at your disposal, your company can optimize inventory management, reduce waste, and keep projects moving forward smoothly.
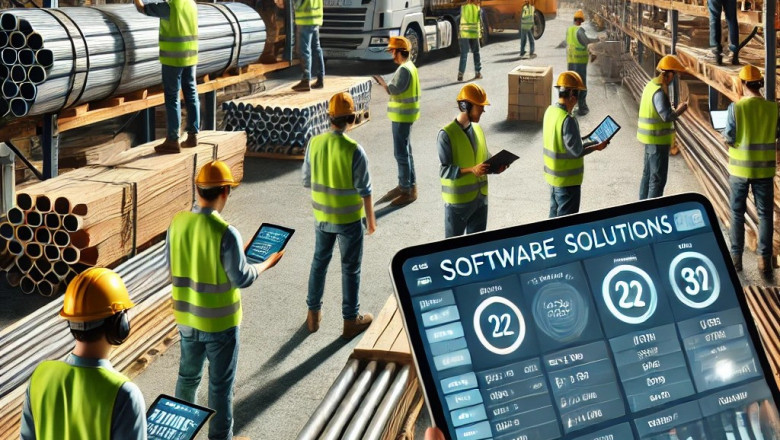

Comments
0 comment